Hot Runner vs Cold Runner Molding Systems
What is the difference between hot runner vs cold runner systems? With the increasing cost of steel and raw materials, supply chain professionals are often looking for options to reduce part prices, cycle times, and material waste. Cold runner systems may be a cost saving solution compared to hot runner systems for the right application. However, hot runner systems may be more efficient long term depending on the production volume. How do you choose between hot runner vs cold runner systems? Read below to find out.
Hot Runner vs Cold Runner Differences
Hot runner systems, a.k.a. “hot sprues,” are molding systems where the molten raw material is physically heated as it is being transferred from the machine’s nozzle into the mold cavity.
Cold runner systems, on the other hand, use unheated channels to direct the molten raw material into the mold cavity. Cold runners prevent the material from curing while within the cold runner unit extending from the molding machine’s injection chamber.
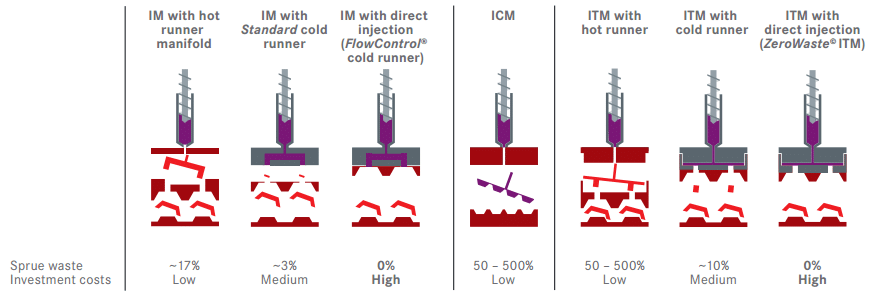
Hot Runner System – Advantages
The major advantages of hot runner systems are the faster cycle times and automation efficiency. Hot runners are best used for high volume runs with consistent quality results. Parts with complex geometries will do well with hot runners. Hot runner systems leave fewer material waste and more consistent quality of products than those produced by cold runners.
Hot Runner System – Disadvantages
The disadvantages to hot runner systems are the long term maintenance and lack of ease in making quick design changes (such as color) compared to cold runner systems. The external and internal heating required by hot runner systems can create more wear and tear on the molding machine as well as increased energy consumption. When choosing hot runner systems, consideration should also be made to the thermal sensitivity of the polymer.
Cold Runner System – Advantages
Cold runner systems have the advantage of shorter set-up times and lower energy consumption compared to hot runners. Typically, a prototype part would benefit from initial samples from a cold runner system as design changes are easier to implement on a cold runner system. Parts having several different color options may benefit from using cold runners for their ease of swapping out colors during production runs.
Cold Runner System – Disadvantages
Some of the disadvantages of cold runner systems are the higher setup cost for tooling, longer cycle time, and more material waste than hot runner systems. Cold runner systems are not recommended for high volume production runs.
Should I Choose Hot Runner or Cold Runner?
Cold runners are a good choice for small volume runs with applications in prototyping and testing color options.
Hot runners tend to be more cost-effective for medium to high volume runs with high repeatability.
Which runner system to choose would usually be decided by the volume of the project. Hot runner systems are the go-to for most injection molding projects due to its reliability and low overhead costs. However, cold runner systems may be more cost effective for smaller quantity projects or prototype testing thanks to its short setup time and flexibility.
Read More
About Coi Rubber Products
Coi Rubber Products, Inc. is a custom manufacturer of molded rubber and plastic components. Coi Rubber has over 28 years of experience in Engineering, Design, Compounding, Prototyping, and Production of molded rubber and plastics. Our capabilities include custom compounding, injection molding, compression molding, transfer molding, extrusions, rubber-to-metal bonding, insert over-molding, and more. We provide large scale production and engineering support to the Automotive, Industrial, Agriculture, Appliance, HVAC industries, and many more. Coi Rubber is IATF 16949:2016 and ISO 9001:2015 certified.
Get a quote for your project: sales@coirubber.com
Visit us at: www.coirubber.com
Have a question? Please fill out the form below to receive information regarding your inquiry. You may also give us a call at (626) 965-9966.
Error: Contact form not found.